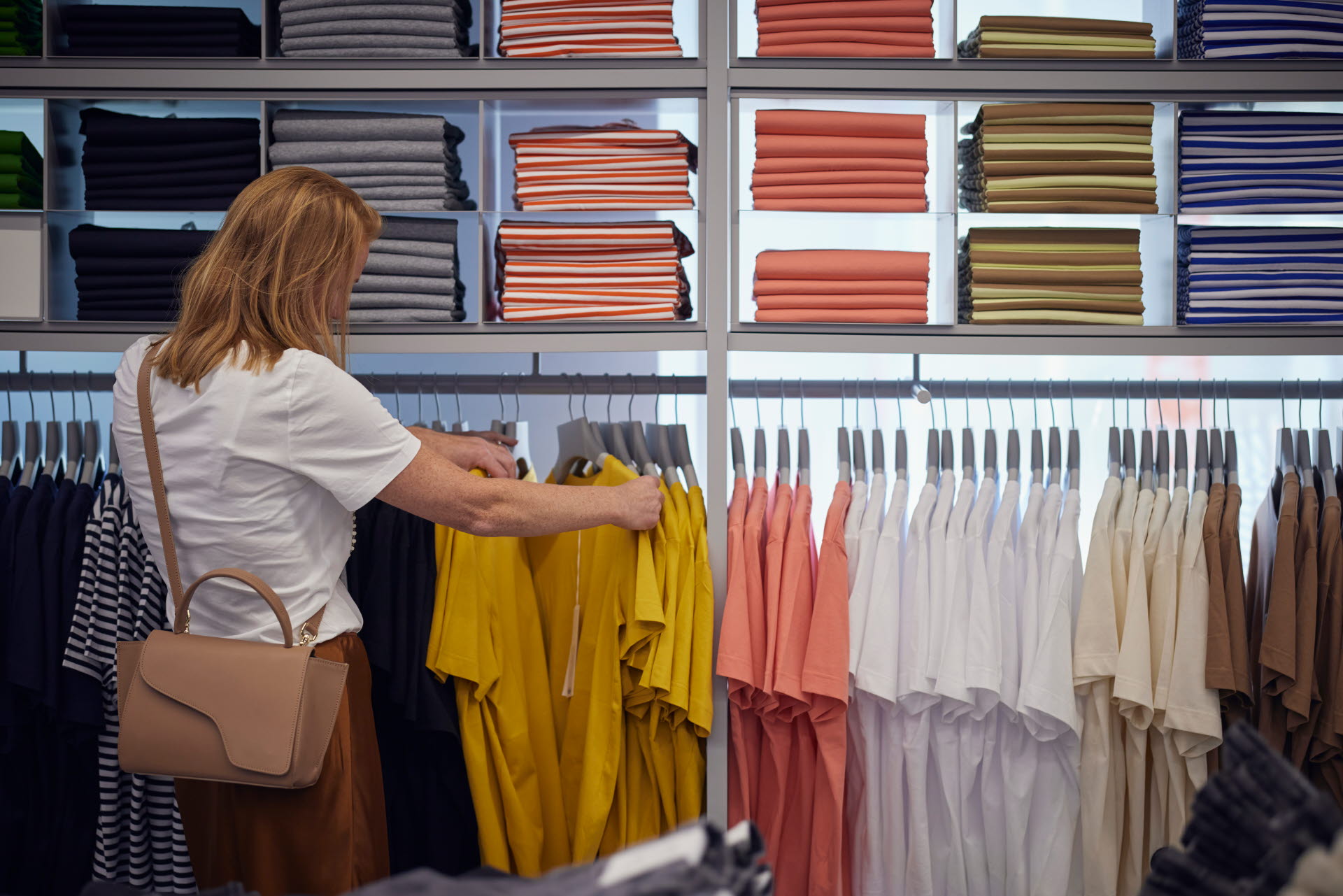
ReSTORE
Der Lebenszyklus der Ladenausstattung wird heute oft vernachlässigt. Stattdessen werden neue Lieferanten beauftragt die alte Ausstattung zu entsorgen. Unser ReSTORE-Programm wurde entwickelt, um genau diese Art von Wertstoffentsorgung zu vermeiden.
ITABs ReSTORE-Programm ermöglicht die Reparatur, Wiederverwendung und Aufarbeitung bestehender Ladenbaumöbel. Dadurch verlängern Sie die Lebensdauer Ihrer Regale, versetzen sie in einen neuwertigen Zustand, sparen Kosten und reduzieren die Umweltbelastung.
Ablauf
Der Grundservice für ReSTORED-Regale ermöglicht Einsparungen von etwa 35 % im Vergleich zu neuen Regalen. Wertstoffe, Kosten, Zeit und Komplexität werden reduziert. Mit drei einfachen Arbeitsabläufe bietet ITAB ressourcenschonende Lösungen für wiederaufbereitete Ladenausstattung (GNFR).
Demontage von Ladenbauteilen
Wir demontieren sorgfältig alle Zubehörteile oder Ladenbauelemente aus der Ausstattung Ihrer Filiale. Anschließend bereiten wir sie für den Versand an ITAB vor.
Sortierung nach Teilenummer
Nach der Demontage sortieren wir die Regale nach kundenspezifischen Teilenummern, um eine effiziente Nachverfolgung und Verwaltung während des gesamten Prozesses zu gewährleisten.

Sortierung nach Aufarbeitung, Wiederverwendung und Recycling
Alle Komponenten werden auf ihre Eignung zur Wiederaufbereitung oder zum Recycling geprüft und entsprechend sortiert. Teile, die nicht wiederverwertet werden können, werden recycelt, um Materialien oder Komponenten zurückzugewinnen.
Rückführung und Reinigung
Die zur Aufarbeitung vorgesehenen Komponenten werden einem gründlichen Reinigungsprozess unterzogen, um Schmutz, Dreck oder Rückstände, die sich im Laufe der Zeit angesammelt haben, zu entfernen. Diese Rückführung in den Rohmaterial-Zustand oder die rohe Oberfläche bereitet den Gegenstand für die weitere Behandlung oder Bearbeitung vor und verleiht ihm ein sauberes und poliertes Aussehen.
Wiederherstellung & Reparatur
Wiederherstellungs- und Reparaturverfahren werden zur Behebung funktioneller oder struktureller Probleme durchgeführt. Dazu gehören der Austausch verschlissener Teile, die Reparatur struktureller Schäden und die Beseitigung ästhetischer Mängel. Eine sorgfältige Wiederherstellung und Reparatur verlängert die Lebensdauer der Gegenständer und trägt zur Nachhaltigkeit und zum Werterhalt bei.
Oberflächenbehandlung
In der letzten Phase des Aufarbeitungsprozesses liegt der Fokus auf der Verbesserung der Optik und der Haltbarkeit der Gegenstände. Das Auftragen von Schutzbeschichtungen verhindert Verschleiß und Abnutzung, sodass die aufgearbeiteten Gegenstände nicht nur ästhetisch ansprechend, sondern auch widerstandsfähig gegen künftige Beschädigungen sind. Dies sichert ihre Langlebigkeit und Qualität.
Umverpackung
Nach der Fertigstellung werden Ihre „neuen“ Regale sorgfältig verpackt, um Transportschäden zu vermeiden und die Qualität und Unversehrtheit der aufgearbeiteten Regale bis zum Zielort sicherzustellen.
Einlagerung & Wiederverwendung
Wir lagern die ReSTORED-Regale in einem bestimmten, klar abgegrenzten Bereich ein und nehmen sie gemäß den Kundenvorgaben in das Umbauprogramm auf.